

However, as I was handling the resin, I could see the draft resin was quickly curing in the ambient light, so I had to work quickly and pour it back into the bottle as a thin crust of material formed. Everyone in the office became quite aware that I was using the draft resin due to its strong odor, so once the print was finished I endeavored to bottle up as much of the resin as I could, thus limiting the nuisance odor to others in the office. I suspect this might have been a user error, because I had changed the resin from clear to draft: I thought I had asked Preform to recompute the support material structure, but it seems that didn’t happen.Ībove: a view of the test part, printed in draft resin.Ībove: close-up of the rather robust support material connection to the print.Īside from woes trying to remove the part from the support material, the other issues I had with the draft resin is its strong smell, and its sensitivity to ambient light. The main downside was that the part as printed was virtually impossible to remove from its support material. The resin still yielded a part with reasonably crisp lines, although as expected the layers were quite visible. Indeed, migrating the design to the draft resin reduced the print time down to under 4 hours, which was a welcome relief for a quick test print. This was not going to cut it for a quick test print! Fortunately, Formlabs had also sent me a sample of their “draft resin”, which advertises itself as a way to rough out quick, low-resolution prints. The design I had chosen was quite large, requiring over 18 hours to print in clear resin. So, I went and downloaded a couple of popular-looking prints from the Internet and loaded them into the latest version of the Preform software. The Form 3 build platform is a little larger than the Form 1, but it turns out there are a number of good reasons for the extra size, which we’ll get into later.īefore taking the whole machine apart, I decided I’d give it at least one test print.
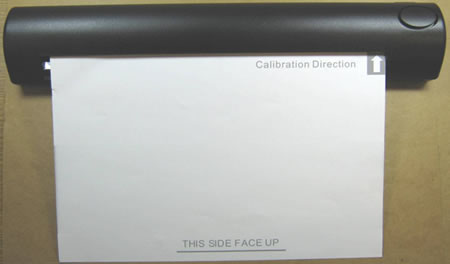
My first impression of the Form 3 was, “wow, this is a big machine”.Ībove is a Form 3 next to a Form 1 for size comparison. I always learn an immense amount while taking apart their machines, and it’s also been very satisfying to watch their engineering team grow and mature over the years. With the recent release of the Form 3, I was asked by Formlabs if I wanted to do another teardown, and of course I jumped on the opportunity. It’s been my privilege to do teardowns on both the Formlabs Form 1 and Form 2.
